2017年,“单辊自适应堆焊修复装置”第一次上岗开工,这是一款通过离线编程,即可实现焊枪数控、多维堆焊的电焊机器人,轻松驾驭着需要多人协作的复杂电焊作业。据方大特钢建安公司电焊高级技师甘荣刚介绍,这台机器人的工作效率非常高,以前需要4个电焊工连续工作5天才能完成的焊接任务,现在只需技术人员编写好程序,由1个电焊工操作和监控,仅4天内就能完成,解决了传统人工焊接高强度、低效率的根本难题。

“单辊自适应堆焊修复装置”就出自甘荣刚领衔的方大特钢“甘荣刚劳模创新工作室”,这是方大特钢倾力打造的“双室”示范平台之一。该工作室自2012年成立以来,一直致力于研究并推广电焊方面的新技术、新工艺,围绕电焊质量和效率进行攻关与改进,先后培养出上百名电焊技能高手,无数匠心巧思在这里盘桓、落地。截至目前,该工作室已陆续推出数十款承担不同复杂工序的电焊机器人,累计获得4项发明专利、37项实用新型专利。
机器人走上生产流水线,是传统产业数字化转型及智能化升级的必然趋势,不仅象征着技术和生产的革新,更是对传统工人角色的重新定义。如今,在建安公司的钢构厂房,利用机器人替代传统手动焊接上岗作业,已成为方大特钢制作及修复大型构件的主导方式。工人们逐步从繁重的手工操作中解脱出来,转而从事更智能的技术操作、更精细的管理工作。
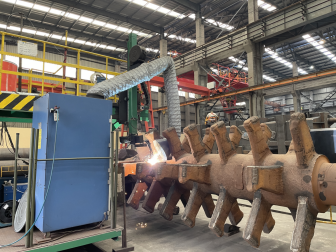
走进炼铁厂烧结区域,台车装载着烧结矿“全年无休”地驶动着,为其加油的工人要忍受50摄氏度的高温,弓背作业一整天,才能为整辆台车完成注油。今年11月,经过5个多月自主研发的“烧结台车自动注油机器人”已熟练上岗,这款机器人仅用2小时就能完成整辆台车的注油,经反复优化,注油准确率已经超过90%,并在不断提升。下一步,将把注油机器人的操作程序连接到主控室,实现在“空调房”的远程操控。
来到轧钢生产线终点,已经不见穿梭在钢材之间,脑力计数、手动焊牌的工人,“螺纹钢焊接挂牌机器人”正在为12—40mm螺纹钢进行挂牌,它通过快速识别螺纹钢端面、统计支数、打印号牌信息以及焊接号牌,每小时可焊接80捆螺纹钢,并达到99.9%的焊挂牢固率及100%的准确率,避免了因手工操作可能带来的误差和质量问题。
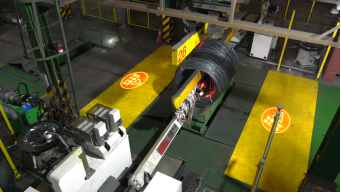
诸如此类的机器人研发并非一蹴而就,而是方大特钢对新时代产业工人队伍建设改革的实践探索,是对工人自主研发的鼓励和支持,是来自工人对生产环境和工作方式的深度思考。在方大特钢,这场机器人引发的系列变革,是企业和工人之间的“双向奔赴”。
“痛点产生需求,需求推动创新,我们这里研发的机器人,都是来自一线工人的需要,为了解决他们工作中的痛点”,方大特钢建安公司副总经理谢雨田表示。
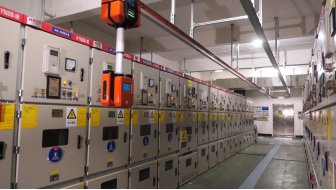
基于一线工人工作中的痛点和需要,方大特钢倾力打造“劳模创新工作室”“技能大师工作室”,按照有领衔人、有团队、有场地实施、有项目攻关、有创效标准,发挥示范效应,引领技术创新,经由分析、改造、研发、攻关,逐一击破各种难点,并使工作室成为带动更多员工钻研技术、参与创新的孵化器。
机器人逐步覆盖劳动强度大、工作模式常态化、作业往复频次高的区域,既为工人提供了更加安全、舒适的工作环境,降低了员工劳动强度、提高了工作效率,也让企业形成自主创新的精神内核,促进企业向智能化、数字化转型发展。
如今,在方大特钢的生产一线、制造前沿,既有尖端技术和先进设备,也有把蓝图变为现实的能工巧匠。